Introduction:
Research for the Re-Newall pages began in the Autumn of 2021, and they were last updated in October 2023. If you are aware of any errors, or would like to add further details or personal memories, please email david@newall.org.uk.
Important Note. Please be aware that we are unable to provide Service Manuals, Operating Instructions, Assembly Drawings or Electrical/Hydraulic/Pneumatic Schematics for any of the machines and instruments manufactured by the Newall Group; we simply do not have access to them. We are unable to help with the repair, refurbishment or operation of any of the products. All the data that we hold is available for free download from the “References” pages that can be found within the relevant sections on the Companies/Divisions tab.
Our knowledge of this company division is rather sketchy and has been pieced together from newspaper reports, various Newall brochures and personal memories/feedback from some of our contributors. On this page we may refer to “the company” but it is unclear whether it became a separate company in its own right, or always remained a division of Newall Engineering.
Whatever its corporate structure, it began life in 1948 as the Used Machine Division (UMD) of the Newall Engineering Company, operating from a very cold and draughty hangar on Conington airfield, about 10 miles south of the Newall Engineering factory in Old Fletton, Peterborough. Its original purpose was to re-precision machine tools of Newall manufacture only.
This airfield (known then as Glatton airfield) had been constructed in 1943 for the American 8th Air Force 457th Bomb Group to launch bombing attacks on Germany during World War II. The airfield ceased military operations and was put into “care and maintenance” in April 1946 and closed as an operational airfield soon after. Much of the old airfield was restored to agriculture, but two runways were retained and became the core of what is now known as Peterborough Business Airport. The following photograph shows a Newall jig borer arriving at the airfield and being off-loaded, ready to be taken into the hangar for refurbishing work to begin.
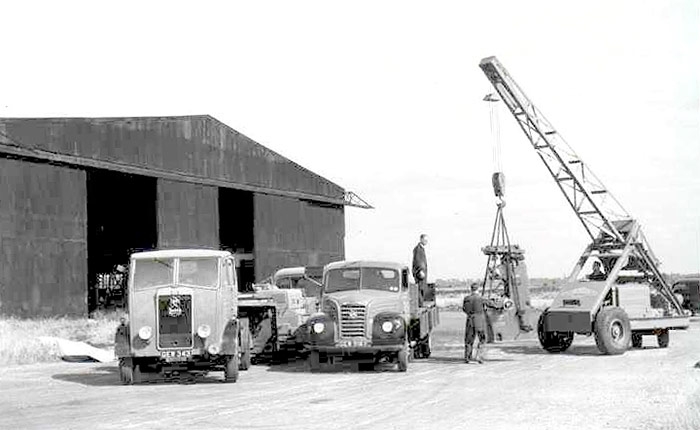
The division expanded considerably over the next few years, and began rebuilding machines such as grinders, borers and planers from other manufacturers. By 1957, UMD sales had increased ten-fold and a brand new factory was built just off Oundle Road in Peterborough, specifically to house the Used Machine Division, which then vacated the airfield premises. However, sales of new Newall machines were also increasing, such that the original Newall Engineering factory in Old Fletton (the No. 1 factory) could not cope with the increased demand and they soon took over part of the new factory and subsequently elbowed out the Used Machine Division to other premises, and the Oundle Road factory became the Newall Engineering No. 2 factory. With the construction of a new road running along the western side of the factory, it was referred to, rather confusingly, as either the Oundle Road factory or the Shrewsbury Avenue factory. For much more detail on the factories themselves please have a look at our Newall Engineering Factories page. The following images show the general appearance of the new UMD factory on Oundle Road and a view of the jig borer fitting section.
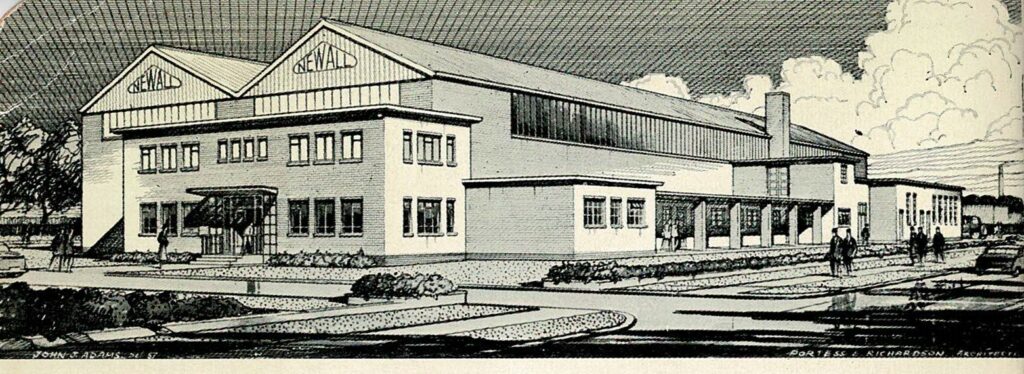
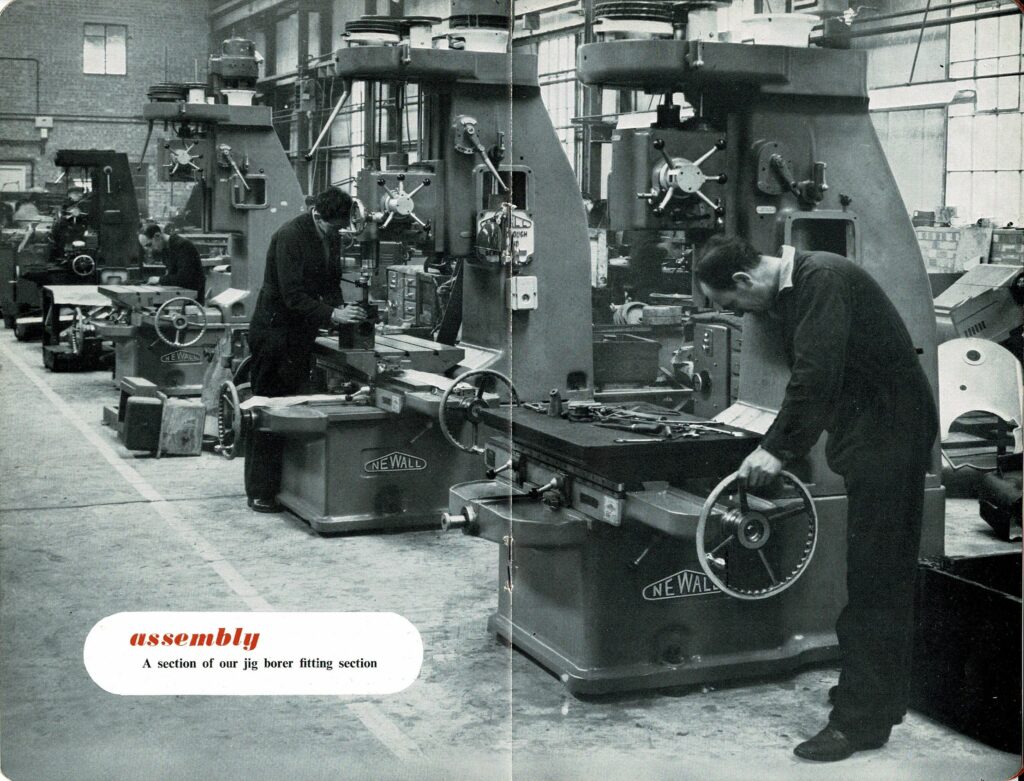
The photo of the jig borer fitting section is taken from a Newall Used Machine Division sales booklet, kindly made available to us by the family of the late Charlie Newman, who was a turner at Newall Engineering. This booklet has been a source of very useful information and we thank them for making us aware of it. You can download it here.
We believe the Used Machine Division occupied the Padholme Road (No. 3) factory for a while, before transferring operations to South Luffenham, about 20 miles north-west of Peterborough.
According to the Wikipedia South Luffenham web page, the mill was originally built in 1890 as a steam-powered grain mill. During the Depression, the mill was acquired by Cadge & Coleman, but became uneconomic and was just used as a distribution centre until 1927. It stood empty for some years, then was briefly used for the manufacture of clips for cartridges before the Ryvita company used it for biscuit manufacture until 1966, coinciding with the closure of the railway station and sidings. Newall took on the premises soon afterwards. The site was accessed by turning immediately right as you crossed the level crossing and following an old dirt track to the old mill and the large new assembly shop. It was tucked out of the way, close to the river Chater where employees would sometimes enjoy a lunchtime swim. Today (October 2023), the site is occupied by Linecross Ltd.
The following photo shows the machine assembly shop there. [[with thanks to Ray Morris]]
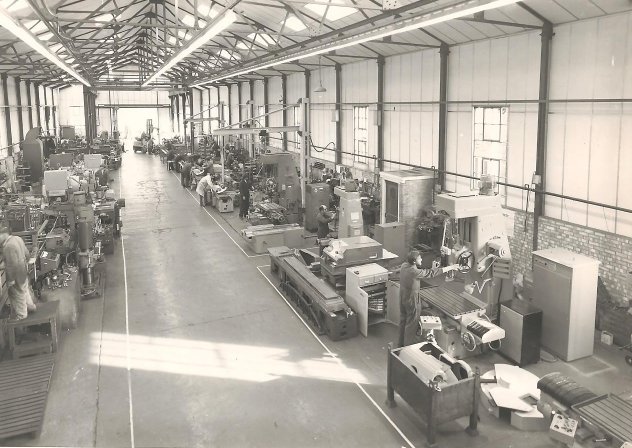
At the time the above photo was taken, the company was described as the Newall Factored Machine Division. In more recent times it became known as the Re-Newall Division (a nice play on words), or simply as “Re-Newall”.
Peter Garratt got in touch to explain that during his time as an employee at South Luffenham in the early 1970’s, their main work was the remanufacturing of crankshaft grinders for Ford, British Leyland and Skoda, some of which had already seen over 40 years’ use. Some machines were significantly re-designed to suit the new Ford V6 engine blocks instead of the original 4-cylinder in-line engines. There were real tax advantages for customers if they chose to re-use old machines instead of investing in brand new ones, so business was brisk. You can see Peter’s recollections of his time with the company on our Memories page.
In October 2023 David Dixon discovered our website and wrote to tell us about his time at Re-Newall (or as he remembers it, UMD, Used Machine Division). You can read the contents of his message on our Memories page, which included the names of some of those he worked with. After a bit of prompting, David came up with a list of all the people he could remember working there 50 years ago. Here is the list:
- Malcolm (“Sticky”) Plumb – draughtsman
- David Trowel
- Len Knight – fitter
- John Smith – fitter
- Alan Ives – fitter
- Roy Bartram – bed scraper
- Martin Bell – electrician
- Victor Crowson – electrician
- David Dixon – centre-lathe turner
- Morris Bradley – centre-lathe turner
- Arthur Corby – centre-lathe turner
- Austin Bland – cylindrical grinder
- Tony Haggie – universal milling m/c
- Michael Bradshaw – paint shop
- Lou Tibbett – storeman
- Sid Ray – mechanical saw/steel stock supervisor
- Peter Garrett – apprentice
In addition to the above local employees, David tells us that the following personnel transferred from the Peterborough factory:
- Ken Collinson – general manager
- Geoff Sawyer – fitting supervisor
- Christopher Craddock – Machine shop supervisor
- Arthur Capon – purchasing
- Ken Barber – fitter/commissioning new machine tools
- Alec Rook – fitter
- “Rigger” Rigby
- Tony Hall – electrician
There was a Ford Transit minibus, driven by Ken Barber from Sawtry every morning (including Saturdays) to South Luffenham, picking up all the original Newall workmen. The local employees nicknamed it “The Monkey Wagon”, a name that stuck over all the years. Eventually, another bus was provided for the Stamford workers too.
[[ David went on to relate the following story of the traumatic journey of two completed machines on their way to the Skoda works. ]]
The Great Skoda Crankshaft Grinders Catastrophe.
The Newall Used Machine Division won an order from Skoda for two crankshaft grinders, one for grinding the main bearings the other for grinding the big end bearings for their Skoda cars range in 1974. Two used crankshaft machines were acquired and converted to their new use. Signed off by Skoda, they were placed in two small bungalow-sized wooden crates by a sub contractor who specialised in heavy export containers; they were massive and a large crane arrived to load them onto the specialist low loaders.
This is when the trouble started. Leaving the South Luffenham factory involved a left turn and slightly uphill to the level crossing just a few metres away. The second Low Loader grounded on the crossing blocking both the road and the Leicester to Stansted railway line. Fortunately we could turn right in our cars and go home another way. The next day we arrived at work and the crossing was clear, so we could enter the works. That was the last, we thought, of the Skoda crank grinders. How wrong we were!
The two crankshaft grinders arrived at the Czechoslovakian Skoda factory and were unloaded. Shock horror!! Both packing cases were upside down! During the unloading at the docks or somewhere, they had been turned over, despite all the labelling showing the right way up!
Engineers from South Luffenham were sent to Czechoslovakia to inspect them and it was then that all the costly damage could be assessed. Volunteer fitters were selected from the factory to go and live in Czechoslovakia near the Skoda works and repair the damage. It took many weeks.
Back at South Luffenham, we in the machine shop had unlimited overtime to replace both leadscrews and leadscrew nuts plus all the other bent, costly items. I worked many hours on the new parts plus the daily work as well but we finally got it all done and our engineers returned home safely, with the grinders passed off by Skoda.
The experience related by the Czech engineer team on their return was one of grim conditions at Skoda. The factory had a dirt floor, prisoners worked in cages as the cars on the production line passed. The food wasn’t very appealing and every Sunday the red team beat the white team at football. The Czech workers were a friendly bunch despite their communist masters but our engineers were glad to return home.
[[ There must be more of you ex-Luffenham people out there who could help us out with a few more stories like David’s. We would love you to tell us about those times. Please don’t be shy!]]